In fitness for Service applications, a series of 3D laser scans are captured on site through our high definition 3D digital capture technique that can be processed instantly for analysis. This rapid process gathers great quantities of field information in a short time.
3D Laser Scanning
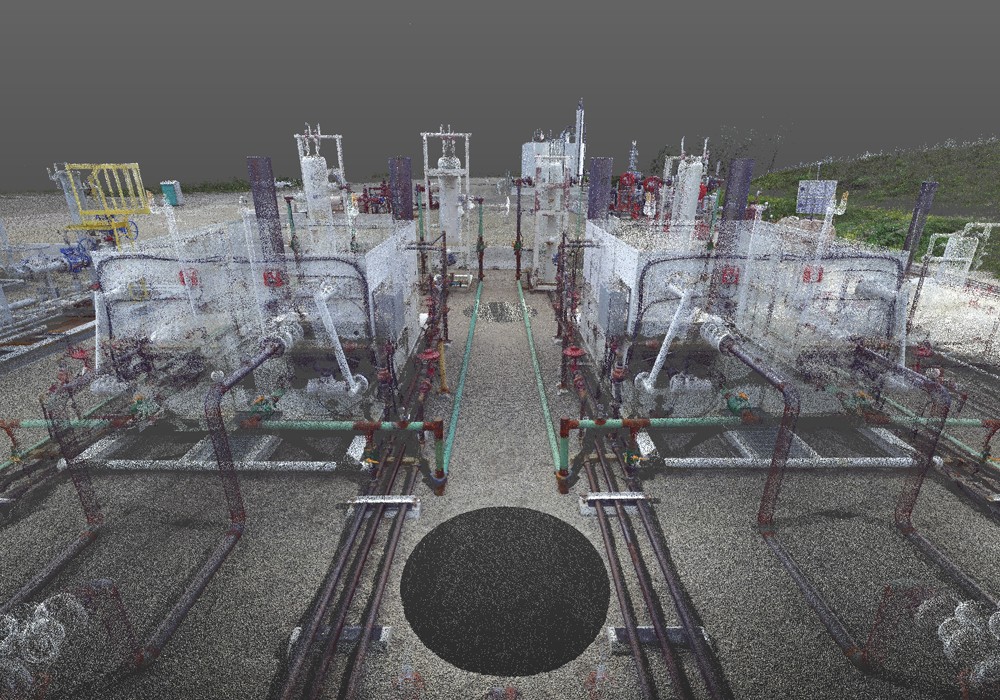
3D Laser Scanning
3D Laser Scanning is a non-contact, non-destructive technology that digitally captures the shape of physical objects using a line of laser light. 3D laser scanners create “point clouds” of data from the surface of an object. In other words, 3D laser scanning is a way to capture a physical object’s exact size and shape into the computer world as a digital 3-dimensional representation.
3D laser scanners measure fine details and capture free-form shapes to quickly generate highly accurate point clouds. 3D laser scanning is ideally suited to the measurement and inspection of contoured surfaces and complex geometries which require massive amounts of data for their accurate description and where doing this is impractical with the use of traditional measurement methods or a touch probe.
Laser scanning is the fastest, most accurate, and automated way to acquire 3D digital data for reverse engineering. Again, using specialized software, the point cloud data is used to create a 3D CAD model of the part’s geometry. The CAD model enables the precise reproduction of the scanned object, or the object can be modified in the CAD model to correct imperfections. Laser Design can provide a surface model or the more complex solid model, whichever results are needed for the application.
3D laser scanners measure fine details and capture free-form shapes to quickly generate highly accurate point clouds. 3D laser scanning is ideally suited to the measurement and inspection of contoured surfaces and complex geometries which require massive amounts of data for their accurate description and where doing this is impractical with the use of traditional measurement methods or a touch probe.
Laser scanning is the fastest, most accurate, and automated way to acquire 3D digital data for reverse engineering. Again, using specialized software, the point cloud data is used to create a 3D CAD model of the part’s geometry. The CAD model enables the precise reproduction of the scanned object, or the object can be modified in the CAD model to correct imperfections. Laser Design can provide a surface model or the more complex solid model, whichever results are needed for the application.
3D Scanning Services
AEC Applications
Oil & Gas Applications
Analysis Applications
Key areas for application include
- 2D & 3D As-built documentation
- 3D Modeling Services
- Clash Detections
- Aid in inspections
- Deformation analysis
- Tank Calibrations
- Volume Calculations
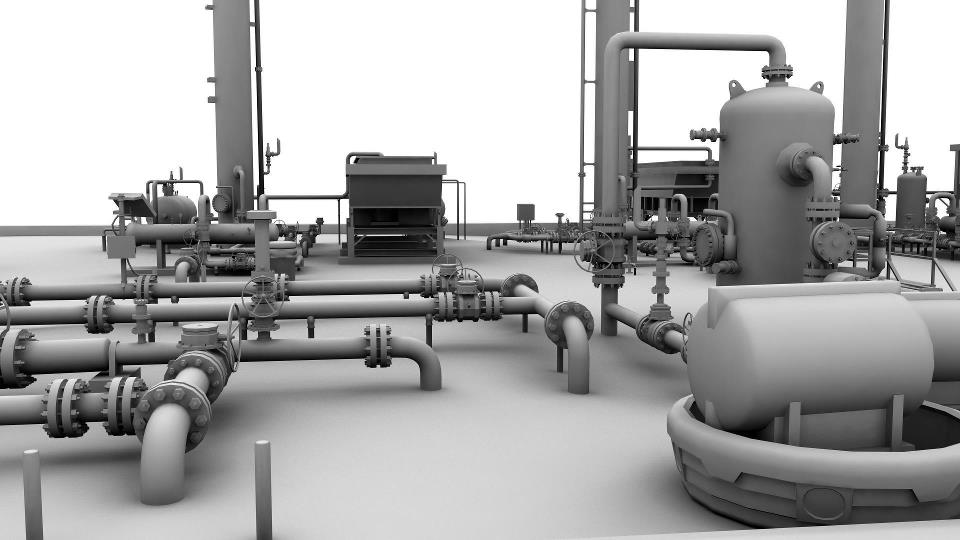
CONTACT INFO
- Address: MIddle East Commercial Centre Office #40, FIfth Floor Madinat AL Umal, Al Khobar Kingdom of Saudi Arbia.
- E-mail: info@sintechs.com